Vehicle System Integration
Vehicle System Integration
Vehicle System
Integration
Vehicle System Integration
Vehicle Electrification Systems
Vehicle System Integration brings together various subsystems and components to ensure they work harmoniously within the vehicle. This process focuses on testing, validating, and fine-tuning each part to optimize performance, safety, and reliability, creating a seamless and efficient vehicle system.
Vehicle System Integration brings together various subsystems and components to ensure they work harmoniously within the vehicle. This process focuses on testing, validating, and fine-tuning each part to optimize performance, safety, and reliability, creating a seamless and efficient vehicle system.
Vehicle System Integration brings together various subsystems and components to ensure they work harmoniously within the vehicle. This process focuses on testing, validating, and fine-tuning each part to optimize performance, safety, and reliability, creating a seamless and efficient vehicle system.
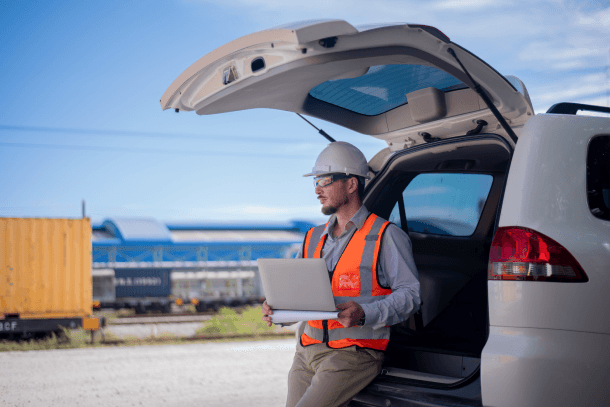
Vehicle Integration Testing
Vehicle Integration Testing
Vehicle Integration
Testing
Vehicle Integration Testing
Ensure that installing the controller being tested does not overload the vehicle’s CAN bus(es).
Verify correct wiring between the vehicle and the controller being tested.
Confirm that the controller receives the expected CAN messages from other vehicle ECUs at the correct rate, with proper data type, length, scaling, and range.
Check that the controller accurately reads driver inputs connected to it.
Ensure that the controller can correctly operate the vehicle actuators it controls.
Validate that the controller meets overall vehicle performance requirements. For example, testing a brake controller to confirm it can decelerate the vehicle at a specified rate.
Ensure that installing the controller being tested does not overload the vehicle’s CAN bus(es).
Verify correct wiring between the vehicle and the controller being tested.
Confirm that the controller receives the expected CAN messages from other vehicle ECUs at the correct rate, with proper data type, length, scaling, and range.
Check that the controller accurately reads driver inputs connected to it.
Ensure that the controller can correctly operate the vehicle actuators it controls.
Validate that the controller meets overall vehicle performance requirements. For example, testing a brake controller to confirm it can decelerate the vehicle at a specified rate.
Ensure that installing the controller being tested does not overload the vehicle’s CAN bus(es).
Verify correct wiring between the vehicle and the controller being tested.
Confirm that the controller receives the expected CAN messages from other vehicle ECUs at the correct rate, with proper data type, length, scaling, and range.
Check that the controller accurately reads driver inputs connected to it.
Ensure that the controller can correctly operate the vehicle actuators it controls.
Validate that the controller meets overall vehicle performance requirements. For example, testing a brake controller to confirm it can decelerate the vehicle at a specified rate.
Customer Training
Customer Training
Customer Training
Customer Training
Our personnel routinely offer direct, in-person support to customers, primarily during project integration testing phases and at key project milestone handovers. Additionally, we provide topic-specific training sessions tailored to customer project needs, which may include guidance on off-the-shelf OpenECU™ products or on new software and hardware developments. We also offer in-vehicle initial calibration, system commissioning, and manufacturing support services.
Our personnel routinely offer direct, in-person support to customers, primarily during project integration testing phases and at key project milestone handovers. Additionally, we provide topic-specific training sessions tailored to customer project needs, which may include guidance on off-the-shelf OpenECU™ products or on new software and hardware developments. We also offer in-vehicle initial calibration, system commissioning, and manufacturing support services.
Our personnel routinely offer direct, in-person support to customers, primarily during project integration testing phases and at key project milestone handovers. Additionally, we provide topic-specific training sessions tailored to customer project needs, which may include guidance on off-the-shelf OpenECU™ products or on new software and hardware developments. We also offer in-vehicle initial calibration, system commissioning, and manufacturing support services.
Solutions
Solutions
Solutions
Solutions